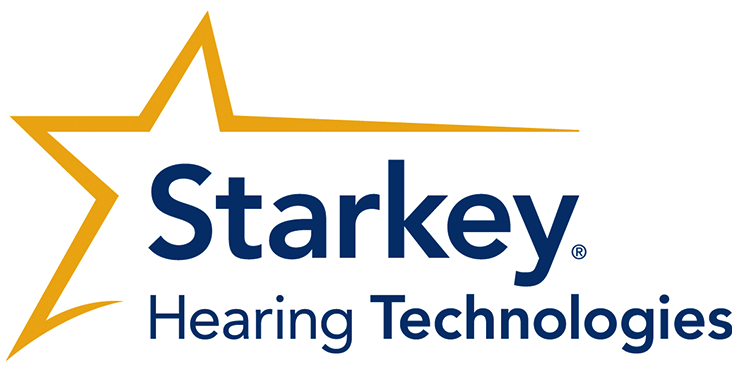
Starkey Hearing Technologies
As a Manufacturing Process Engineer in hearing aid manufacturing, I work on developing and improving the processes used to build high-quality products.
Hi, my name is Abtin Tehrani, and I’m a Mechanical Engineer currently working as a Process Development Engineer at Starkey Hearing Technologies, where I contribute to improving and validating manufacturing processes in a fast-paced, regulated environment.
I graduated with a degree in Mechanical Engineering from the University of Minnesota-Twin Cities, and have over six years of hands-on experience in manufacturing environments. My background includes time spent as a machine operator, quality inspector, and now as an engineer, which gives me a well-rounded perspective on production workflows, process optimization, and cross-functional collaboration.
My passion for mechanical systems and problem-solving began at a young age—whether it was taking apart RC cars or helping out in my father’s auto parts store. That early curiosity has grown into a strong foundation in engineering principles, hands-on troubleshooting, and a continuous drive to improve how things are made.
During my time at the University, I completed two internships at The Toro Company in mechanical design and advanced manufacturing, where I worked on real-world product development and process improvement projects. These experiences, combined with my current engineering role, have helped shape my career path and solidified my interest in driving innovation in manufacturing.
This portfolio highlights some of the projects and experiences that showcase my journey so far. I’m excited to continue building my career in an environment where I can contribute meaningful solutions, learn from experienced professionals, and grow as an engineer.
As a Manufacturing Process Engineer in hearing aid manufacturing, I work on developing and improving the processes used to build high-quality products.
For my ME 2011 Intro to Engineering class, I demonstrated my mechanical arm project at the robot show event. During my time working at Boston
For the ME 4045W Design Projects class, I worked in a team of five to design an automated clipping basket for green mowers. The purpose of this project was to automate a device to collect, measure, and disperse grass clippings. In the current design (Figure 3), the operator needs to frequently detach the basket to check the clipping level and manually dump it when it is full. The goal of our project was to create a prototype device that could replace the manual disposal of collected grass clippings with an automated mechanism.
In the summer of 2022, I obtained my first internship with The Toro Company as an Advanced Manufacturing Engineering Intern at their global headquarters in Bloomington, Minnesota, USA. I worked as a full-time employee during the summer, and upon my request and my manager's approval, my internship was extended for an additional nine months during my school semesters.
Besides collaborating with the Indian team to generate process plans, I worked with designers in our department to design fixtures for various assembly purposes and to create technical drawings for different parts and assemblies
In Mechanical Design Engineering Internship role, the first project assigned to me by the management team was designing a new housing for the next generation of batteries used in operating lawn mowers, snow blowers, leaf blowers
The other project in my Mechanical Engineering internship position was to design a bracket for holding a battery charger (Figure 15) on the wall.
As a Process Development Engineer, I support new product development by validating manufacturing processes, designing custom fixtures in Creo, and developing tooling for new assembly lines. I work cross-functionally with engineering teams and contribute to risk assessments, FMEA sessions, and the creation of clear, structured workflows for validation activities.
Worked as a Design Engineering Intern in the summer of 2023, responsible for designing prototypes for the next generation of batteries and a wall-mount bracket for holding a battery charger. Collaborated closely with senior engineers to develop new products and improve existing designs. Conducted laboratory investigations to analyze competitor batteries. Thoroughly documented findings to present to senior managers and engineers.
Worked for one year on a manufacturing engineering team, primarily responsible for supporting production workflows by creating 3D illustrations for assembly lines. Assisted designers in creating technical drawings for various parts and assemblies. Participated in VR meetings that focused on using virtual simulations to enhance assembly line efficiency and reduce downtimes.
Served as a Medical Inspector and Assembler at Boston Scientific for over a year, contributing to the assembly and testing of medical devices in a cleanroom environment, with a focus on endoscopy equipment. Demonstrated proficiency by efficiently managing operations across five stations within three months.
Held a medical inspection position at Medtronic to assemble and inspect balloons and stents in the cleanroom area. Conducted final testing to ensure compliance with engineering specifications. Managed all relevant medical device information by organizing data using Excel.
Worked as a mechanical operator for two years, tasked with building truck power inverter systems according to engineering blueprints. Identified and resolved assembly discrepancies, leading to reduced rework and increased efficiency on the assembly line.
Bachelor's degree, Mechanical Engineering
Associate of Science - AS, Mechanical Engineering